磨料去毛刺——为工件打造完美表面质量的秘密武器
在工业生产中,尤其是金属加工领域,毛刺的出现几乎是不可避免的。毛刺是一种由工件加工过程中产生的锋利边缘或突起物,通常存在于切割、冲压、铣削等工序后。尽管毛刺本身并不影响工件的功能,但它们却可能带来一系列的问题,如影响工件的组装、使用寿命和外观质量等。因此,去毛刺成为了提升工件质量和制造效率的重要环节。
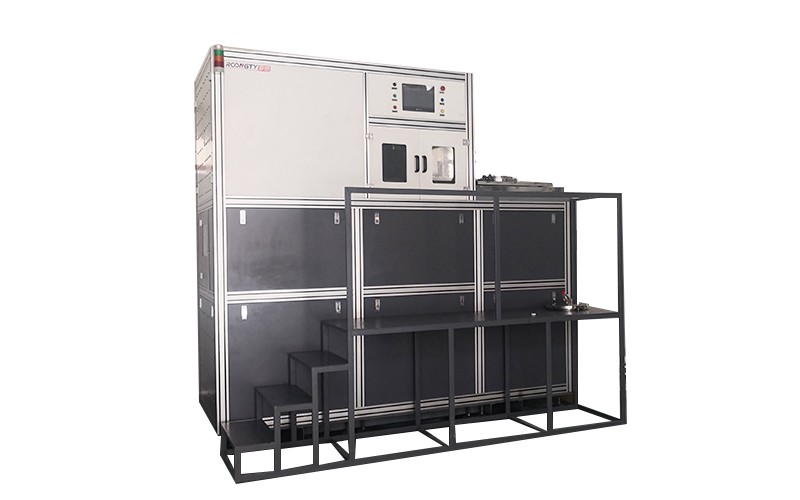
其中,磨料去毛刺技术作为一种先进的表面处理方法,因其高效、精确和环保的特点,逐渐成为了制造业中不可或缺的技术手段。磨料去毛刺不仅能够有效清除工件表面的毛刺,还能改善表面光洁度,为产品增添附加值。通过对磨料去毛刺技术的深入了解,我们能够更好地应用这一技术,提升生产效率和产品质量。
磨料去毛刺的工作原理
磨料去毛刺技术,顾名思义,就是通过磨料对工件表面进行打磨,从而去除毛刺。磨料通常是一些颗粒状的物质,具有较高的硬度和耐磨性。当这些磨料与工件表面接触时,通过高速的相对运动,磨料的颗粒与工件表面发生摩擦,进而去除毛刺。
在具体的操作过程中,磨料去毛刺可以采用不同的方式进行,如喷砂法、磨料刷法、振动磨料法等。每种方式都有其独特的优势和应用场景,能够针对不同的工件材质和毛刺类型进行选择。喷砂法适用于大面积的毛刺去除,能够均匀去除工件表面的毛刺;而振动磨料法则更适合精密零件的处理,能够在不损伤工件的情况下,去除微小的毛刺。
磨料去毛刺的优势
高效性:磨料去毛刺技术相较于传统的人工去毛刺或机械去毛刺方法,具有显著的高效性。磨料能够快速而均匀地处理工件,减少了人工操作的时间和精力,提升了生产效率。尤其是在大批量生产中,磨料去毛刺能极大地缩短生产周期。
精确性:磨料去毛刺不仅能够去除工件表面的毛刺,还能够对工件表面进行细致的抛光处理。通过控制磨料的类型、颗粒大小、喷射压力等参数,可以精确控制去毛刺的效果,确保工件表面质量达到预期要求。这对于一些对表面质量有严格要求的产品,如精密仪器零件、汽车零部件等,尤为重要。
环保性:与传统的化学去毛刺方法相比,磨料去毛刺更具环保优势。磨料去毛刺不需要使用化学溶剂或有害物质,减少了对环境的污染。磨料本身通常是可回收使用的,这进一步降低了生产成本,提升了企业的环保形象。
适用性强:磨料去毛刺技术适用于各种不同材质的工件,尤其是金属、陶瓷、塑料等材料。无论是钢铁、不锈钢,还是铝合金、铜合金,磨料都能有效地去除毛刺,保证工件表面的光滑度和精度。
磨料去毛刺的应用领域
磨料去毛刺技术的应用范围非常广泛,涵盖了各个行业。以下是几个主要的应用领域:
汽车制造业:在汽车零部件的生产中,精密的表面质量直接影响着零部件的性能和耐用性。通过磨料去毛刺技术,可以去除汽车零部件表面的毛刺,保证其装配精度和使用寿命。例如,发动机零部件、刹车系统、车身结构件等,都需要经过磨料去毛刺处理,确保其表面光洁、无瑕。
电子行业:在电子产品的生产中,许多元器件的表面也容易产生毛刺,尤其是在金属外壳和电路板的加工中。磨料去毛刺能够有效去除这些微小的毛刺,保证产品的性能和安全性。例如,手机外壳、电脑零部件等都需要进行磨料去毛刺处理,以确保其表面无毛刺、不易生锈或损坏。
航空航天领域:航空航天器的零部件要求精度高、表面质量好。磨料去毛刺能够帮助去除这些高精度零件表面的微小毛刺,提高零件的可靠性。例如,飞机发动机、航天器外壳等都需要进行细致的去毛刺处理。
医疗器械行业:医疗器械对精度和安全性要求极高,任何细小的毛刺都可能影响器械的使用效果,甚至导致安全隐患。磨料去毛刺能够确保医疗器械表面光滑,避免毛刺对人体的伤害。例如,手术器械、注射器等都需要经过磨料去毛刺处理。
磨料去毛刺技术在各行各业的广泛应用,使得其成为了现代制造业中不可或缺的重要技术。磨料去毛刺技术的选择和应用也需要根据具体的工件特性、生产需求以及成本控制等因素来综合考虑。以下将进一步探讨磨料去毛刺的技术要点、注意事项以及未来发展趋势。
磨料去毛刺的技术要点
磨料的选择:磨料的种类、颗粒大小和硬度直接影响到去毛刺效果的优劣。常见的磨料包括钢丸、陶瓷颗粒、玻璃珠等,不同类型的磨料适用于不同材质的工件。在选择磨料时,需要考虑工件的材质、毛刺的类型以及所需的表面质量。例如,对于硬度较高的金属材料,可能需要选择更硬的磨料,而对于较软的材料,则可以选择较为柔软的磨料,以避免对工件表面造成损伤。
工件的夹持与定位:在磨料去毛刺的过程中,工件的夹持与定位十分重要。工件必须固定牢靠,以避免在处理过程中产生位置偏移,导致毛刺去除不均匀或损伤工件表面。夹具的设计要符合工件的形状和尺寸,确保磨料能够均匀地作用于工件表面。
设备的选择:磨料去毛刺通常需要借助专业的去毛刺设备,如喷砂机、振动磨机、滚筒磨床等。不同设备的工作原理和处理效果各有差异,因此在选择设备时,需要综合考虑工件的生产批量、表面质量要求以及处理时间等因素。对于小批量生产,振动磨机可能更为适合;而对于大批量生产,喷砂机或滚筒磨床则能够提供更高的生产效率。
操作参数的控制:磨料去毛刺的效果不仅与磨料的选择密切相关,还与操作参数如磨料流量、喷射压力、加工时间等有关。通过合理调整这些参数,可以精确控制去毛刺的深度和效果。例如,喷砂压力过大会导致工件表面产生过度磨损,而压力过小则可能导致去毛刺不彻底。因此,在操作过程中,需要严格控制这些参数,以达到最佳的去毛刺效果。
磨料去毛刺的注意事项
避免过度磨损:在使用磨料去毛刺时,必须避免对工件表面造成过度磨损。过度磨损不仅会降低工件的使用寿命,还可能导致其尺寸发生变化,影响产品的精度。因此,在进行磨料去毛刺时,应根据工件的材质和要求选择合适的磨料和参数,避免不必要的磨损。
定期更换磨料:磨料在长期使用过程中会逐渐磨损,其去毛刺效果会逐渐降低。因此,定期更换磨料,确保磨料的颗粒保持锋利和均匀,可以有效提高去毛刺的效果。
保持设备清洁:磨料去毛刺设备在长期使用后,磨料和工件的残留物可能会影响设备的正常运行。因此,定期清洁设备,确保其处于良好的工作状态,是提高生产效率和产品质量的重要保障。
磨料去毛刺的未来发展趋势
随着制造技术的不断进步,磨料去毛刺技术也在不断发展。未来,磨料去毛刺将朝着更加智能化、自动化的方向发展。借助人工智能和大数据技术,未来的磨料去毛刺设备将能够实现更精确的控制和更高效的生产,进一步提升生产效率和工件质量。环保型磨料和绿色生产工艺的引入,也将使磨料去毛刺技术更加符合可持续发展的要求。
总结来看,磨料去毛刺技术凭借其高效、精确、环保等优势,已经成为了现代制造业中不可或缺的重要技术手段。通过合理选择磨料、优化操作参数和设备,企业能够在确保产品质量的大幅提升生产效率,满足日益增长的市场需求。