抛光去毛刺,提升产品品质的秘密武器
在当今的工业制造领域,随着生产技术的不断进步,产品的质量已成为各行各业关注的焦点。而在确保机械零部件和产品质量的过程中,抛光去毛刺技术无疑发挥着至关重要的作用。无论是在汽车制造、航空航天、电子产品、医疗器械,还是在日常消费品中,抛光去毛刺技术都扮演着一个不可忽视的角色。它不仅关乎产品外观的精致与美观,更关系到产品的使用性能与安全性。
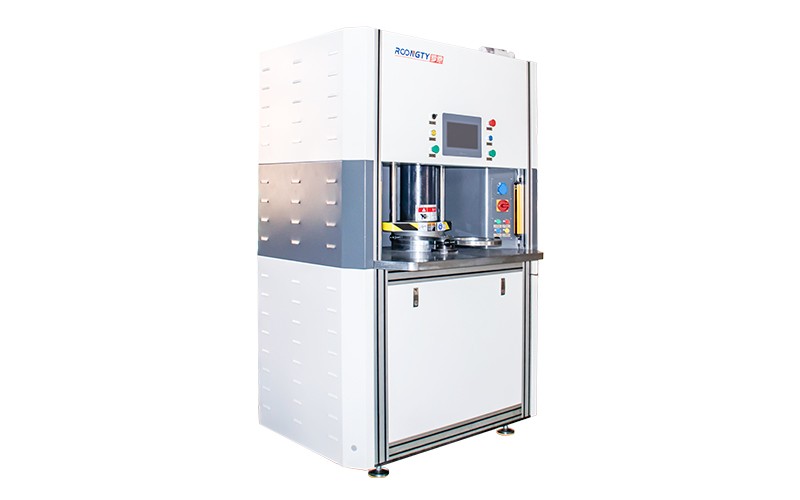
何为抛光去毛刺?
抛光去毛刺,顾名思义,是通过物理或化学的方法去除产品表面加工过程中产生的毛刺,使得产品表面更加光滑、精细。这一过程不仅能够改善产品的外观,更能减少毛刺可能带来的危害,如刮伤、损坏、降低配件的配合精度等。
在制造过程中,毛刺的产生几乎是不可避免的。它通常是在加工过程中,切削工具与工件表面接触时产生的微小凸起。虽然这些毛刺在初期可能不会影响产品的基本功能,但它们往往会影响到产品的组装精度、耐用性以及安全性。因此,去除毛刺,不仅是提升产品质量的必要步骤,更是确保产品符合安全标准的基本要求。
抛光去毛刺的重要性
提升外观质量
对于很多产品而言,外观是消费者选择购买的一个重要因素。尤其是在手机、家电、汽车等消费品中,精致的外观和光滑的表面能够提升产品的附加值,增强市场竞争力。抛光去毛刺使得表面更加平整光滑,避免了因毛刺造成的瑕疵,使产品看起来更加精美,提升了消费者的购买欲望。
提高机械性能
表面光滑的工件不仅美观,而且能够提升机械性能。去毛刺后,产品表面不仅更加坚固,而且可以减少摩擦,降低磨损,延长产品使用寿命。例如,在机械配件中,如果毛刺没有去除,可能会导致配件的结合处不精确,增加运转时的摩擦力,甚至可能导致配件的损坏。通过抛光去毛刺处理,能够显著减少这些问题,确保产品的精密度与稳定性。
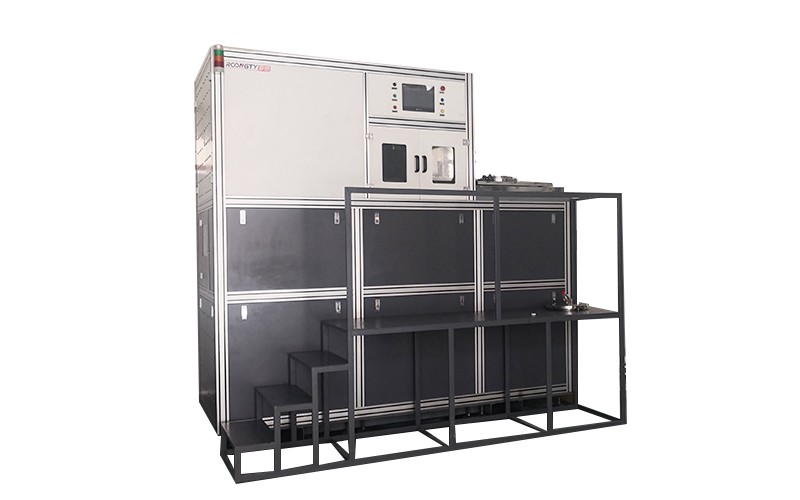
提高安全性
毛刺可能带来不小的安全隐患。在一些高精度的医疗器械或者航空航天领域,毛刺往往会导致产品无法精确组装,甚至可能造成意外故障,影响安全性。而通过抛光去毛刺处理,不仅能避免这些隐患,还能有效提高产品的可靠性和使用寿命。尤其是在医疗器械中,去毛刺处理能够减少对人体的伤害,确保产品的使用安全。
抛光去毛刺的技术选择
抛光去毛刺的技术选择,通常取决于产品的材质、形状、尺寸以及生产的批量等因素。常见的去毛刺技术包括手工抛光、机械抛光、电解抛光、化学抛光等。
手工抛光
手工抛光是最传统的去毛刺方式,主要依靠人工使用砂纸、抛光轮等工具对产品表面进行摩擦处理。这种方法适用于对精度要求不高的小批量生产,或是形状复杂、难以用机械处理的工件。手工抛光能够精细地处理细节,但效率较低,且对于大批量生产来说,成本较高。
机械抛光
机械抛光是一种通过机械设备来去除毛刺的方式,常见的设备有抛光机、抛光轮等。这种方法适用于大批量生产,且能够保持一定的处理精度和一致性。机械抛光的效率较高,适用于大多数金属及塑料工件,广泛应用于机械零部件的抛光。
电解抛光
电解抛光是一种利用电解反应原理,通过电流作用去除金属表面微小毛刺的技术。此方法适用于不锈钢、铝合金等金属工件,能够在去除毛刺的提高表面的光洁度和耐腐蚀性。电解抛光常被应用于高端机械零部件、医疗器械等对表面要求极高的产品。
化学抛光
化学抛光是利用化学溶液通过化学反应去除金属表面毛刺的一种方法。该技术适用于一些难以通过机械或电解方式处理的工件,能够实现均匀的抛光效果。化学抛光的优点是处理过程中不会产生机械力,适用于精密加工要求较高的场合。
抛光去毛刺的优势
无论采用哪种技术手段,抛光去毛刺的最终目标都是提升产品质量,确保其符合生产标准与客户要求。抛光去毛刺不仅可以提高产品的外观质量和机械性能,还能降低生产成本、提升产品的市场竞争力。在精密加工领域,抛光去毛刺技术是每一个制造商必须掌握的核心技能之一。
在接下来的部分中,我们将深入探讨抛光去毛刺技术的未来发展趋势以及如何选择合适的抛光去毛刺设备,帮助企业提升生产效率和产品质量。
随着现代制造业的发展,抛光去毛刺技术的应用不仅仅局限于传统的金属加工领域,越来越多的新兴材料和先进制造技术的出现,推动了这一技术的持续创新与进步。
抛光去毛刺的未来发展趋势
智能化与自动化
随着人工智能和自动化技术的发展,抛光去毛刺设备正在朝着智能化、自动化的方向发展。智能化设备能够通过内置的传感器和数据分析系统,实时监控抛光过程中的各项参数,确保处理效果的稳定性和一致性。自动化系统可以大幅提高生产效率,减少人工干预,降低人为错误的风险。未来,智能化和自动化技术将成为抛光去毛刺设备的重要发展趋势。
环保与绿色制造
随着环保要求的提高,未来的抛光去毛刺技术将更加注重环保与绿色制造。传统的抛光去毛刺过程常常需要使用大量的化学溶剂和磨料,这不仅增加了生产成本,也对环境产生了一定的污染。而新型的环保抛光技术将减少化学品的使用,采用更加绿色环保的材料与方法。例如,采用高效能的环保磨料和水基溶剂,减少对环境的影响,符合可持续发展的生产要求。
纳米技术的应用
随着纳米技术的发展,纳米抛光技术也逐渐应用于高精度的去毛刺处理中。通过纳米技术,可以在微观尺度上对材料进行处理,实现更加精细、均匀的表面光滑效果。纳米抛光技术不仅能够去除微小毛刺,还能够提升材料表面的硬度、耐磨性和耐腐蚀性。因此,未来的抛光去毛刺技术将更加注重微米甚至纳米级的精度要求,满足高端行业对表面质量的苛刻要求。
高效多功能设备
未来的抛光去毛刺设备将不再仅仅局限于单一的功能,而是趋向高效多功能化。例如,集抛光、去毛刺、去氧化皮等多种表面处理功能于一体的设备将成为行业的新趋势。这种设备不仅可以提高生产效率,降低设备投资成本,还能够满足不同工艺要求的生产需求。
如何选择合适的抛光去毛刺设备?
选择合适的抛光去毛刺设备,是确保加工质量和生产效率的关键。企业在选择设备时,通常需要考虑以下几个因素:
材料类型
不同材料对抛光去毛刺的要求不同,例如,金属材料和塑料材料的抛光方式和技术需求有所不同。了解所需加工材料的特性,选择相应的抛光设备和技术,可以更有效地去除毛刺,并保证加工精度。
产品形状与尺寸
不同形状和尺寸的产品,可能需要不同类型的抛光设备。例如,对于复杂形状的零部件,手工抛光或小型的机械抛光设备可能更为适用;而对于大批量生产的标准零件,自动化抛光设备则能提供更高的生产效率。
生产批量
生产批量的大小,直接影响到选择抛光去毛刺技术的选择。对于小批量生产,手工抛光或小型机械抛光设备可能足够;而对于大批量生产,自动化、高效的抛光设备则能够提供更好的效率和一致性。
成本与效益
企业在选择设备时,需要综合考虑设备的投资成本和长期效益。一方面,设备的采购价格需要符合企业预算;另一方面,设备的生产效率、使用寿命及其后续维护成本也要被纳入考量范围。
总结
抛光去毛刺技术作为提升产品品质的重要手段,已经被广泛应用于各行各业。从外观到性能,从安全性到耐用性,抛光去毛刺技术直接影响着产品的质量和市场竞争力。随着制造业技术的不断创新,未来的抛光去毛刺技术将更加高效、智能、环保,帮助企业在激烈的市场竞争中脱颖而出。
通过选择适合的抛光去毛刺设备和技术,企业可以大大提升生产效率,确保产品的品质和可靠性,实现持续的创新与发展。在未来的制造业中,抛光去毛刺技术将继续发挥其不可替代的重要作用,为产品质量和行业发展注入源源不断的动力。