震动抛光技术——赋能精密加工的未来
在现代制造业中,如何提高产品的表面质量和加工效率,一直是技术研发的重点。震动抛光技术,作为一种新兴的表面处理方式,正逐渐取代传统的抛光方法,成为提升产品质量的重要手段。震动抛光是一种通过利用研磨介质在加工件表面进行高速振动摩擦的方式,达到去除表面粗糙度、改善表面光洁度的技术。随着技术的不断成熟和设备的优化,震动抛光在精密加工中的应用逐渐被各行各业所青睐。
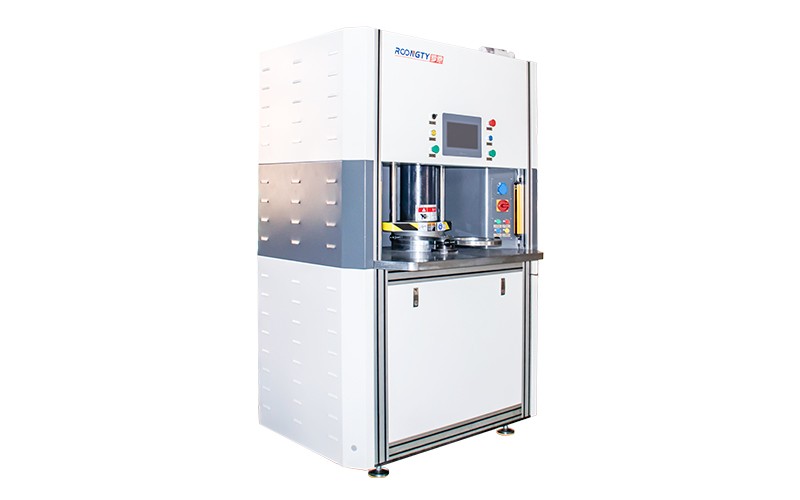
震动抛光的原理非常简单,却极为有效。它通过一台震动设备将工作件与研磨介质放入同一个容器中,在高速振动下,研磨介质对工件表面进行摩擦和碰撞,从而去除工件表面的氧化层、毛刺、锈斑等不平整的部分,最终获得光滑、细腻的表面效果。震动抛光不仅能处理金属,还可以应用于陶瓷、塑料、玻璃等多种材质的表面处理。
与传统的手工抛光或机械抛光相比,震动抛光具有明显的优势。它能够大幅提升加工效率。在传统的抛光过程中,人工操作往往需要耗费大量时间和精力,而且很难确保每个细节的完美处理。而震动抛光通过机械化操作,能够在较短时间内完成大批量的处理工作,大大提高了生产效率。震动抛光能保持表面的一致性和精度,尤其适用于小型、复杂形状的零件加工。震动抛光的工作原理使得研磨介质能够均匀地分布在工件表面,避免了人工操作时可能出现的偏差,使每个工件的表面光洁度都达到相同标准。
震动抛光的适用范围非常广泛。无论是在珠宝、汽车配件、电子产品,还是医疗器械、航空航天领域,震动抛光都能够发挥其独特的优势。在珠宝加工中,震动抛光可以使金属表面光滑且有光泽,提升珠宝的外观品质;在汽车零部件中,震动抛光不仅能够去除毛刺和氧化层,还能减少零部件之间的摩擦,提升零件的使用寿命;在电子行业,震动抛光常常应用于精密零件的表面处理,能够达到非常高的光洁度,保证产品的性能和外观。
随着工业制造对精度和效率的要求不断提高,震动抛光技术在行业中的应用前景更加广阔。许多制造商已经开始意识到震动抛光在提升产品质量和加工效率方面的重要作用,因此这一技术的市场需求也在不断增加。未来,随着技术的进一步进步,震动抛光有望在更多高精度和高要求的领域得到应用,推动制造业向更加高效和智能化的方向发展。
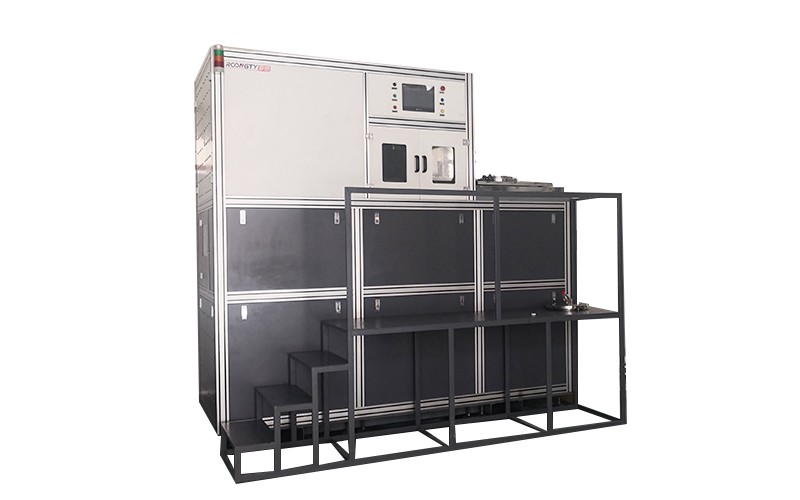
震动抛光技术的未来发展方向,不仅仅在于提升加工效率和表面质量,更多的是通过与智能化、自动化技术的结合,推动整体制造水平的提升。随着物联网、大数据、人工智能等技术的兴起,震动抛光设备的智能化已经成为发展的一大趋势。未来的震动抛光设备将能够通过实时监控和数据分析,对工件的处理过程进行精确控制,实现自动化和个性化的定制化生产。
例如,结合传感器和数据采集技术,震动抛光设备可以实时监测工作件的表面状态,并根据需要自动调整振动频率、研磨介质的类型及数量,从而实现最佳的抛光效果。这不仅能够减少人工干预,还能大幅提升产品的一致性和精度。人工智能算法也能够帮助设备更好地预测工件加工过程中的问题,避免出现过度磨损或不均匀处理等情况,从而进一步提高生产效率。
在未来,震动抛光技术的应用还将向着多功能、高精度和高自动化方向发展。比如在航空航天领域,对于发动机零部件、飞机涡轮叶片等高精度要求的零件,震动抛光能够去除表面缺陷并提升零部件的抗腐蚀性能,同时保证其在长时间使用中的稳定性和高效性。随着对表面处理质量要求的不断提高,震动抛光将成为许多高精度行业中不可或缺的技术手段。
震动抛光在环保方面的优势也不容忽视。相比传统的抛光方法,震动抛光过程中的粉尘、噪音和废料较少,符合现代制造业对环保的要求。采用封闭式的震动抛光设备,能够最大限度地减少对环境的污染,确保生产过程的绿色可持续性。
震动抛光技术的不断创新和发展,正引领着制造业向着更高效、更环保、更智能的方向迈进。在智能制造的浪潮中,震动抛光无疑是一个不可忽视的重要技术,其在未来的发展潜力巨大,必将在全球制造业中占据更加重要的地位。
震动抛光技术作为一种先进的表面处理工艺,已经在多个行业中得到了广泛应用,并且随着技术的不断进步,其在精密加工中的优势将更加突出。无论是在提升生产效率,还是提高产品质量,震动抛光都展示了强大的竞争力。未来,随着智能化、自动化的进一步推进,震动抛光技术必将为全球制造业带来更多的变革和突破。