板材去毛刺——提高生产效率,确保产品质量的关键步骤
在现代制造业中,板材作为基础材料,被广泛应用于各行各业。无论是在汽车制造、建筑结构、电子产品,还是家电行业,板材的加工处理都起着至关重要的作用。而其中一个不可忽视的环节——板材去毛刺,则直接影响着最终产品的质量和生产效率。
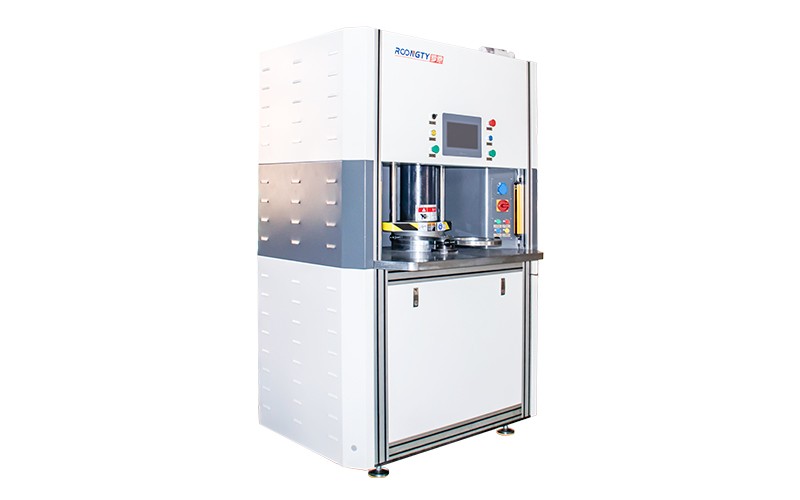
什么是板材去毛刺?
板材去毛刺是指在板材切割、冲压或激光切割等加工过程中,材料边缘所产生的不规则、尖锐或不平整的小颗粒、毛刺被去除的过程。这些毛刺如果不及时去除,不仅会影响产品的外观和精度,还可能导致产品的使用性能降低,甚至出现安全隐患。因此,去毛刺对于提升产品质量,保证加工精度,确保后续工序的顺利进行具有不可或缺的作用。
毛刺的产生与影响
毛刺通常在板材经过切割、冲压等工序后产生。切割过程中,板材受到高温或压力的作用,边缘会出现变形、裂纹或多余的金属残留物,这些就是所谓的毛刺。毛刺的存在会影响到板材的装配精度,尤其是在精密装配过程中,毛刺可能导致配件不匹配,从而影响整体产品的质量。
毛刺对后续加工过程也具有不小的影响。例如,后续的焊接工艺可能因为毛刺的存在而发生熔接不良或接头不牢固的情况;在电镀或喷涂过程中,毛刺可能导致涂层不均匀,影响美观和防腐效果。
板材去毛刺的重要性
提高产品质量
去除毛刺不仅能改善板材的外观,还能提高产品的性能。在许多高精度要求的行业中,毛刺会影响装配精度,甚至可能导致生产过程中出现故障。因此,去毛刺成为了保证产品质量的重要环节。
提升生产效率
如果毛刺没有及时去除,后续加工过程中可能会出现一系列问题,导致停机、返工,浪费时间和资源。通过有效的去毛刺处理,可以避免这些问题的发生,减少生产线上的停滞时间,提高生产效率。
增强产品的使用安全性
一些产品在使用过程中可能会与其他部件发生接触,若毛刺未清除干净,可能会导致操作不便、损坏甚至发生安全事故。例如,在汽车制造过程中,毛刺可能会影响车身零部件的装配精度,进而影响车辆的安全性能。
延长设备使用寿命
板材上的毛刺如果不去除,会对加工设备造成损伤。刀具、模具等加工工具在处理毛刺时容易磨损,增加了设备的维护成本。因此,及时去毛刺有助于延长设备的使用寿命。
板材去毛刺的方法
根据不同的生产需求和板材的材质、厚度等特点,常用的去毛刺方法也各不相同。以下是几种常见的去毛刺方法:
机械去毛刺
机械去毛刺是通过各种机械设备进行的,包括滚轮、砂带、刷轮等。这些设备能够在一定压力下对板材表面进行处理,去除毛刺。机械去毛刺具有高效、经济的特点,适用于大批量生产。
气流去毛刺
气流去毛刺是通过高压气流将板材表面的毛刺吹掉。这种方法适用于精度要求较高、表面不允许留下划痕的场合。气流去毛刺的速度较快,但对设备的要求较高。
化学去毛刺
化学去毛刺通过浸泡或喷洒化学溶液来去除毛刺。这种方法适用于较为复杂的工件,尤其是表面有多个小孔或复杂形状的工件。化学去毛刺能够对不同材质的毛刺进行处理,但需要严格控制化学品的浓度和处理时间。
电解去毛刺
电解去毛刺是通过电解反应将板材表面金属的毛刺部分溶解。该方法精度高,能够去除微小的毛刺,适用于高精度和复杂形状的工件。电解去毛刺适用于金属板材,尤其是对于不锈钢等材料的毛刺清除效果良好。
激光去毛刺
激光去毛刺是一种新型的高效去毛刺技术,通过激光束的高能量将毛刺部分蒸发掉。该方法具有较高的精度,适用于一些高精度、高难度的工件去毛刺。激光去毛刺的优点是高效且不会对工件本身造成损伤,但设备成本较高。
选择合适的去毛刺方法
在选择去毛刺方法时,企业需要根据板材的材质、厚度、形状以及生产要求来综合考虑。对于批量生产而言,机械去毛刺和气流去毛刺可能是最常见的选择,它们效率高、操作简便;而对于精密要求较高的产品,激光去毛刺和电解去毛刺则更具优势。
不同的去毛刺方法各有优缺点,企业在选择时需要权衡各种因素,包括成本、加工精度、处理速度等,确保既能保证产品质量,又能提高生产效率,降低生产成本。