去内毛刺,打造精致品质——提升产品质量的关键步骤
内毛刺的危害与去除的重要性
在现代工业生产中,内毛刺的存在无处不在。从电子产品到机械零部件,几乎所有精密制造的产品在加工过程中都会产生一定程度的毛刺。内毛刺是指在加工过程中,材料表面或内部由于切割、磨削、冲压等操作所产生的小碎屑、尖锐物。虽然这些毛刺看似微不足道,但它们却可能对产品的性能和外观产生巨大的负面影响。因此,去内毛刺不仅仅是提升产品外观的问题,更关乎产品的使用寿命、性能稳定性以及消费者的安全。
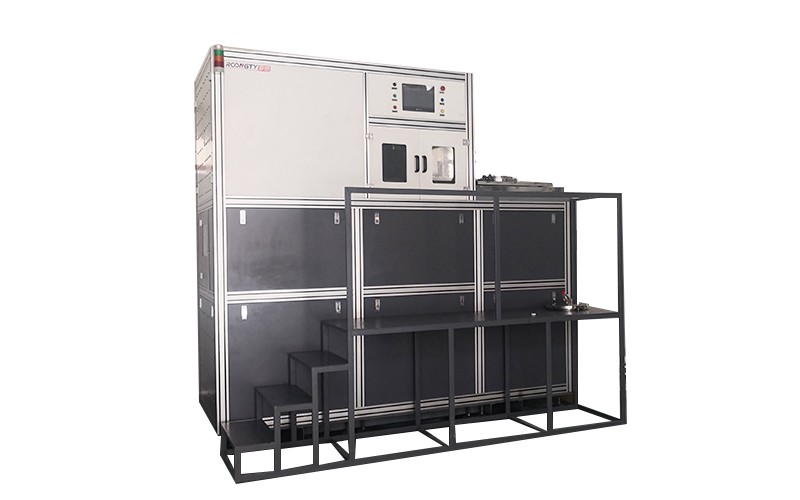
1.1内毛刺的产生
内毛刺的产生是工业加工中普遍存在的一种现象。在金属、塑料、陶瓷等材料的加工过程中,特别是在切割、冲压、铣削等操作中,机械刀具与材料表面发生摩擦、撞击时,材料表面会出现微小的突出部分,这些就是毛刺。而内毛刺则是那些隐藏在产品内腔、深孔或难以触及的部位,肉眼无法直接看到的细小尖锐物。
对于很多精密零部件,尤其是电子产品、汽车配件和航空零部件来说,内毛刺的存在不仅影响外观质量,还可能导致设备卡滞、磨损加剧,甚至直接影响到产品的功能。这种隐患如果未被及时发现并去除,可能会在后续的使用过程中引发严重的质量问题。
1.2内毛刺的危害
1.2.1影响产品性能
内毛刺直接接触到其他部件时,容易导致机械部件之间的摩擦和磨损,从而影响零部件的使用寿命。例如,在汽车发动机零部件中,如果内毛刺未能去除,随着使用时间的延长,毛刺可能导致零部件不平滑,从而加剧磨损,影响发动机的性能和可靠性。
1.2.2增加故障风险
在高精度设备中,内毛刺会导致配合部件卡住,甚至发生故障。例如,在液压设备或气动设备中,毛刺可能会卡住流体通道,导致流体流动不畅,甚至引起系统崩溃,造成安全隐患。
1.2.3降低产品外观
对于一些外观要求极高的产品,内毛刺的存在会严重影响产品的精致程度。特别是在消费电子、家电等行业,消费者对外观的要求愈发严格。如果内毛刺没有去除,产品的外表就会出现瑕疵,从而影响消费者的购买体验,甚至导致品牌形象的下降。
1.2.4加大后期加工难度
内毛刺如果未被及时去除,还会增加后期的加工难度。特别是在需要进行电镀、涂装、焊接等后处理操作时,毛刺会影响涂层的均匀性,甚至导致电镀工艺的失败,影响整个产品的质量。
1.3去内毛刺的重要性
为了避免内毛刺带来的负面影响,及时去除内毛刺是每一个制造商必须关注的问题。去毛刺不仅仅是为了提升产品的外观,更重要的是保障产品的质量与安全性。通过有效的去毛刺工艺,不仅能够提升产品的整体性能,还能够提高生产效率,降低后期修复成本。
目前,随着制造业的快速发展,各行各业对于产品精度和质量的要求越来越高,去毛刺已经成为了产品制造过程中必不可少的一步。特别是在一些高精度的产品中,毛刺的去除成为了提高产品合格率和竞争力的关键因素。
如何高效去除内毛刺
去内毛刺的工作看似简单,但却需要精准的工艺和先进的设备。在实践中,不同材料、不同形状和不同精度要求的产品需要选择不同的去毛刺方法。以下是一些常见且高效的去内毛刺的技术手段。
2.1机械去毛刺
2.1.1切削法
切削法是通过机械刀具对毛刺进行去除的传统方法,适用于平面或易于接触的毛刺去除。切削法常见的工具有砂轮、刀具、刀片等,使用时通过对表面进行切削来去除毛刺。这种方法适用于大多数金属材料,尤其是在需要大规模生产的情况下,切削法的效率非常高。
2.1.2振动去毛刺
振动去毛刺是一种通过振动运动使毛刺与其他工件表面发生碰撞,从而将毛刺去除的技术。该方法适用于去除精密零件和复杂形状的内毛刺。振动去毛刺不仅能去除难以接触到的区域毛刺,还能减少传统切削方法对工件表面造成的损伤。
2.1.3超声波去毛刺
超声波去毛刺利用高频超声波对零部件进行处理,通过产生的微小振动将毛刺去除。这种方法具有很高的精度,能够处理深孔、内腔等复杂部位的毛刺,特别适用于精密零件的去毛刺。超声波去毛刺能够有效降低工件的损伤,同时保持零部件的原始结构和精度。
2.2化学去毛刺
化学去毛刺是一种利用化学反应来溶解或去除毛刺的技术,适用于一些特殊材料或者复杂的零件形状。化学去毛刺常用的技术有酸洗和电化学去毛刺。
2.2.1酸洗去毛刺
酸洗法通过将工件浸泡在酸性溶液中,利用酸的腐蚀作用去除金属表面和内部的毛刺。这种方法适用于大批量生产,特别是对于一些不容易接触的内腔部分,酸洗去毛刺能够有效地完成任务。
2.2.2电化学去毛刺
电化学去毛刺通过在工件上施加电流,使毛刺部分在电解液的作用下溶解。这种方法具有高精度、低损伤的特点,适用于复杂形状和精密零件的去毛刺。
2.3激光去毛刺
激光去毛刺是一种高效、环保的去毛刺技术,采用激光束直接照射到工件表面,通过高温熔化毛刺部分并将其蒸发。激光去毛刺能够精确地控制去除区域,适用于各种材料,尤其是在处理小尺寸或复杂形状的零部件时,具有非常高的精度和效率。
2.4去毛刺设备与自动化
随着工业自动化技术的发展,许多去毛刺操作已经可以通过自动化设备来完成。自动化去毛刺设备可以大大提高生产效率,并减少人工操作带来的误差。现代化的去毛刺设备不仅提高了生产线的工作效率,还保证了去毛刺的质量和一致性。
2.5如何选择合适的去毛刺技术
选择合适的去毛刺技术需要考虑多个因素,包括产品的材料、形状、精度要求、生产规模等。一般来说,在选择去毛刺技术时,要综合考虑效率、成本、精度等因素,确保选择的去毛刺方法能够达到最佳的效果。
通过对内毛刺的有效去除,不仅能够提升产品的外观质量,还能确保产品的安全性和性能稳定性。随着科技的不断进步,去毛刺技术将更加成熟和多样化,成为提升制造业竞争力的重要手段。