提升产品质量,打造完美表面——毛刺处理的重要性与方法解析
随着工业制造技术的不断进步,产品的精密度和质量要求越来越高。尤其是在金属加工、机械制造等领域,毛刺的存在已成为影响产品质量和性能的主要因素之一。毛刺是指在切削、冲压、铣削等工艺过程中,由于工具的作用或金属物料的应力作用,导致工件表面产生的小突起或边缘。这些微小的毛刺虽然看似不起眼,但却会对产品的功能、使用寿命以及美观造成严重影响。因此,毛刺处理在现代制造业中显得尤为重要。
毛刺的产生通常在各种加工工艺中都有可能出现,尤其是在高速切削、冲压、磨削等过程中。尽管它们的形态各异,但无论毛刺的大小,都会影响产品的精度、功能和外观。例如,在电子产品的生产过程中,毛刺可能导致电子元件接触不良,甚至出现短路现象;在汽车制造中,毛刺可能引起机械零部件的卡顿或磨损,缩短零件的使用寿命。因此,去除毛刺不仅是提升产品质量的必要环节,也是确保设备长期稳定运行的关键因素。
常见的毛刺处理方法有机械去毛刺、化学去毛刺、电解去毛刺等多种形式。每种方法有其独特的优势和适用场景,选用合适的去毛刺方式,能达到最佳的处理效果。
机械去毛刺是一种常见的毛刺处理方式,主要通过机械设备对工件表面进行去除。常见的机械去毛刺方法有手工去毛刺、磨光去毛刺和喷砂去毛刺等。手工去毛刺通常适用于小批量生产和对精度要求较低的工件,但其效率较低且劳动强度较大。而磨光去毛刺则通过研磨工具对工件表面进行打磨,能够有效去除较大或较粗的毛刺,常用于精密零件的加工。喷砂去毛刺则是通过高速喷射砂粒,借助砂粒的冲击力去除毛刺,适用于形状复杂的工件。
除了机械去毛刺,化学去毛刺和电解去毛刺也是较为常用的处理方式。化学去毛刺是通过化学反应溶解或软化毛刺的金属,使其从工件表面脱落。此方法适用于大批量生产中对工件的精度要求较高的情况。化学去毛刺能够在不损伤工件本身的情况下去除微小毛刺,对于细小和复杂部位的毛刺去除效果尤为显著。常见的化学去毛刺方法包括酸洗、酸蚀和碱洗等,具有较高的加工效率。
电解去毛刺则是通过电解原理,利用电流作用去除工件表面的毛刺。电解去毛刺适用于形状复杂、细小的工件,尤其在精密零件和薄壁零件的去毛刺上具有独特的优势。该方法能够精确控制去毛刺的深度和位置,避免对工件本体造成任何损害。
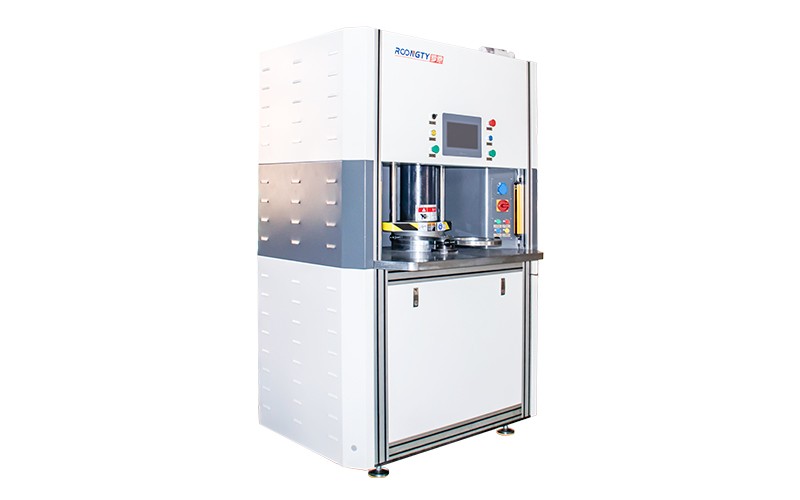
在选择毛刺处理方法时,企业需要根据工件的材质、形状、尺寸以及生产工艺等因素进行综合考虑。对于不同的产品,不同的毛刺去除方法具有不同的优势,选择合适的工艺才能保证最佳的去毛刺效果。
随着制造技术的不断发展,毛刺处理技术也在不断创新和进步。如今,很多企业采用先进的自动化设备和智能化技术来提高毛刺处理的效率和精度。通过机器学习和人工智能技术,企业能够实现精准的去毛刺控制,大幅提升生产效率和产品质量。
毛刺处理不仅仅是制造环节中的一项技术工艺,它对于产品的使用寿命、质量稳定性以及安全性都有着深远的影响。通过科学的毛刺处理方法,企业可以大大减少产品的缺陷,提高产品的市场竞争力,赢得消费者的信赖。
毛刺处理在现代制造业中占据着举足轻重的地位。通过合理的毛刺处理,不仅可以提高产品的质量,还能有效降低生产成本。对于制造企业而言,掌握合适的毛刺处理技术,已经成为提升竞争力的关键之一。在未来,随着技术的不断进步,毛刺处理工艺必将更加精细化和智能化,为制造业的进一步发展注入新的动力。