内孔去毛刺:打造完美产品的关键一步
内孔去毛刺的重要性及方法
在现代精密制造行业中,内孔去毛刺被视为一个至关重要的工艺步骤。无论是汽车、航空、还是医疗器械领域,内孔毛刺的去除都会直接影响到产品的性能和使用寿命。毛刺是一种在加工过程中,材料表面形成的多余部分,它会导致零件的精度偏差,甚至影响装配的顺畅度。在很多高精度的工程中,内孔毛刺不仅是制造缺陷,更可能成为机械故障的根源,因此它的去除显得尤为重要。
为什么内孔去毛刺如此重要?
提高产品质量与精度:
内孔去毛刺是确保产品精度的关键工艺。在许多机械装配中,零件的相互配合需要精确的尺寸和光滑的表面。毛刺不仅会导致尺寸不符,还可能在装配过程中导致摩擦,影响装配效果。通过有效的去毛刺工艺,可以最大限度地提升产品的精度和外观,避免因微小缺陷导致的重大问题。
减少故障隐患:
内孔的毛刺如果没有去除,可能会成为磨损、腐蚀等问题的源头,进一步影响设备的稳定性和安全性。毛刺可能会在运转过程中与其他零部件发生接触,造成不必要的摩擦,甚至引发零件破损。对于高压、高温等复杂环境下的机械设备,毛刺的去除显得尤为重要,因为它直接关系到设备的安全性和可靠性。
提高生产效率:
毛刺的存在可能导致机械零件无法顺利安装或运行,从而延长生产周期,增加人工成本。通过在生产环节中及时有效地去除毛刺,可以确保机械零件的顺畅运作,减少因装配不当或运转不稳定导致的返工,从而提高整体生产效率。
内孔去毛刺的常见方法
去毛刺的方法有很多种,常见的几种方法如下:
机械去毛刺法:
机械去毛刺法是通过机械工具对零件进行加工,以去除内孔的毛刺。常见的工具包括钻头、砂轮、去毛刺刀等,这些工具通过高速旋转、切削等方式去除毛刺。机械去毛刺法通常适用于大规模生产,能够高效去除毛刺,但对于较为复杂的内孔形状和精度要求较高的零件,可能需要较高的操作技巧和设备。
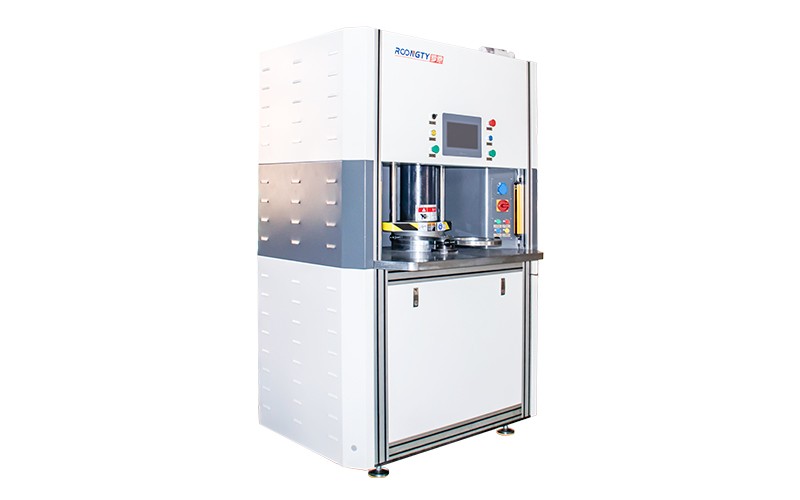
手工去毛刺法:
手工去毛刺法通常使用手动工具,如锉刀、砂纸等,对内孔进行细致打磨。这种方法适用于小批量生产或者对于精度要求较低的零件。虽然手工去毛刺可以实现较高的精度,但由于人工操作的差异,可能会存在一定的误差,并且去毛刺效率较低。
化学去毛刺法:
化学去毛刺法是利用化学溶液的腐蚀性作用去除内孔中的毛刺。这种方法的优势在于能均匀地去除毛刺,尤其适用于形状复杂、难以接触到的内孔。化学去毛刺适用于大规模生产,但其成本较高且需要对化学溶液的控制进行严格管理。
电解去毛刺法:
电解去毛刺法是利用电流通过电解液的化学反应,将毛刺部分腐蚀掉。这种方法的优点在于能够精确去除细小的毛刺,尤其适用于精密零件。电解去毛刺过程中的电流密度和液体温度需要精细调控,以确保去毛刺的效果和零件的表面质量。
激光去毛刺法:
激光去毛刺法通过高能激光束直接作用于毛刺部位,瞬间加热并蒸发毛刺。这种方法的优点是高效且能够在不接触工件的情况下去除毛刺,适用于高精度、高表面质量要求的零件。激光去毛刺设备价格较高,因此在成本可控的前提下,适用于对精度要求极高的领域。
内孔去毛刺的应用领域与未来发展趋势
内孔去毛刺不仅在机械加工中有着广泛的应用,它的技术革新和发展正在逐步影响各行各业。随着科技的进步,越来越多的去毛刺技术被引入并不断优化,带来了更高效、更精确的去毛刺方法。
内孔去毛刺的应用领域
汽车制造:
在汽车制造过程中,内孔去毛刺是确保发动机、变速器、刹车系统等关键零部件可靠性的基础。内孔毛刺如果没有去除,不仅会影响零件的配合精度,还可能影响整个系统的运转稳定性。例如,发动机内部的燃油喷射孔、活塞环槽等位置的毛刺如果没有被及时去除,会导致油路不畅,进而影响发动机的性能。
航空航天:
在航空航天领域,内孔去毛刺尤为重要。飞机发动机、高精密传感器、导航设备等零件的制造需要极高的精度,任何毛刺都会造成设备故障,甚至影响飞行安全。内孔去毛刺工艺对于提高零部件的可靠性、延长使用寿命起到了决定性作用。
医疗器械:
医疗器械领域的零件常常需要精确的内孔加工,如手术器械、植入物等。这些器械需要在体内长时间使用,因此去毛刺不仅要保证零件的精度,还要避免毛刺对人体产生任何危害。毛刺的去除直接关系到医疗器械的安全性和有效性。
精密仪器:
精密仪器的内孔去毛刺要求更高。无论是电子设备、光学仪器,还是实验设备,任何细微的毛刺都会影响到其正常工作。随着高精度设备需求的增加,内孔去毛刺工艺的精密程度也在不断提高,以确保每一个零件都符合最高标准。
未来发展趋势
随着制造技术的不断进步,内孔去毛刺技术也在持续创新。例如,自动化去毛刺技术正逐步代替传统手工操作,提高了去毛刺的效率和精度。智能化去毛刺系统将结合人工智能和大数据分析,进一步提升去毛刺过程的自适应能力和智能控制水平。
未来,环保和节能将成为内孔去毛刺技术发展的重要方向。新的去毛刺方法将更加注重资源的节约和环境保护,例如采用低污染的化学溶液和减少能耗的去毛刺设备。
通过技术的持续创新,内孔去毛刺将不断向高效、环保和智能化的方向发展,以满足不同行业对零部件精度和质量的更高要求。